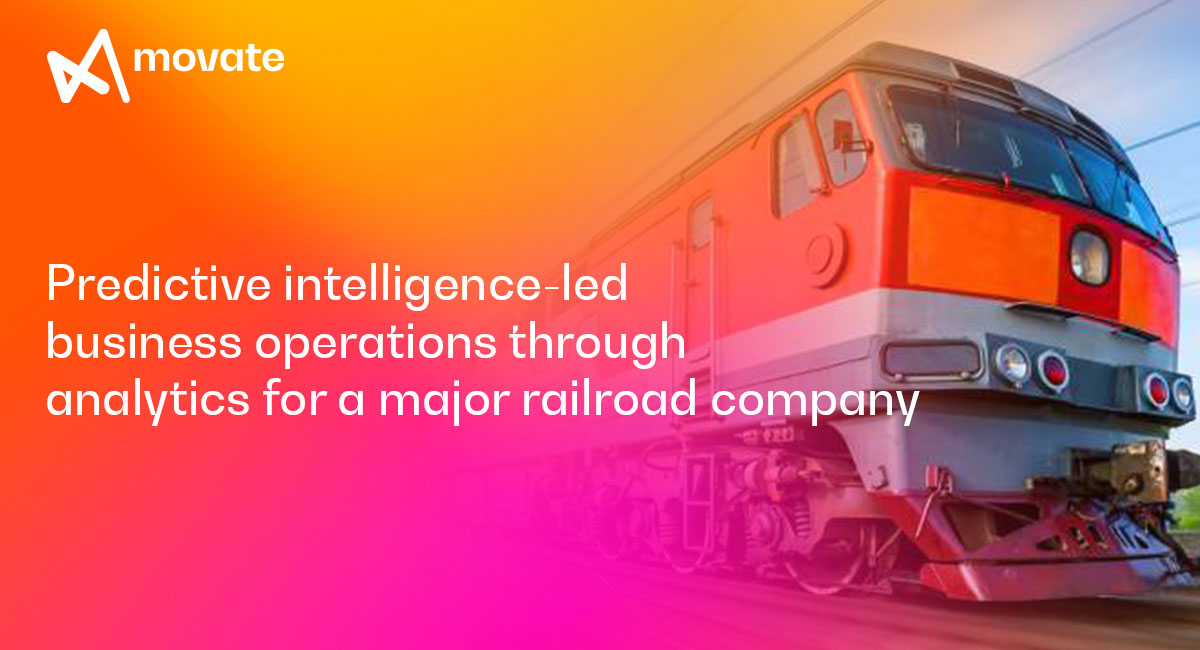
Client Profile
The client is a 150-year-old company that maintains and leases railroad equipment such as locomotives, freight cars, and passenger transit vehicles and manufactures rail braking systems, air-con systems, and rolling stock components.
Client Challenge
The railroad industry has changed over the last decade, with digital technologies were enabling early adopters to be more efficient and competitive. The client’s outdated maintenance methods were manual, inefficient, and expensive: they used a reactive maintenance schedule loosely integrated with daily operations. With enormous capital tied up in their fleet, the client also needed to maximize the return on their investment. revenue lost from equipment that was broken or taken out of service for maintenance was hurting their top line.
Movate Solution
Movate led the client through a digital transformation of their maintenance program. They modernized operations to include an IoT network and provide an agile, three-layered digital services framework to improve operational performance:
- Operational & Engineering Intelligence
- Acoustics and Image Data Analysis
- Monitoring and Maintenance Platform
- Operational & Engineering Intelligence
- Implemented Movate’s Smart Analytics platform to provide real-time insights on critical operational parameters gathered through IoT sensors. This allowed better planning, scheduling, and utilization of rolling stocks.
- Inferred the patterns and analyzed log entries of different maintenance schedules to segregate rolling stocks.
- Generated insights on component history, failure ratios, & failure rates across various component brands. These actionable insights helped in the proactive monitoring of critical functional parameters.
- Acoustics and Image Data Analysis
- Used the Smart Analytics platform to extract acoustic samples of operative machinery, which otherwise was hard to monitor through manual interventions.
- Configured the platform to detect rail fractures, correlate events to verify component health status, and make informed decisions
- Implemented audio analysis to provide acoustic feedback during real-time functioning of key components (e.g. wheels)
- Monitoring and Maintenance Platform
Implemented a platform that focuses on:
- Maintaining and monitoring railroad assets in real-time
- Providing preventive maintenance of critical railroad assets
- Managing schedules and downtimes with no service disruptions
Business Benefits
- Reduce Operational Costs by 25% through digitization of operations through IoT and analytics
- Improve Engineer’s Productivity through digitization of routine tasks, enabling them focus on core competencies
- Enhance Mean-Time-To-Repair Rates by 35%, ensuring timely and proactive maintenance schedules fully integrated with daily operations.
Movate, formerly CSS Corp, is a digital technology and customer experience services company committed to disrupting the industry with boundless agility, human-centered innovation, and a relentless focus on driving client outcomes. Recognized as one of the most awarded and analyst-accredited companies in its revenue range, Movate helps ambitious, growth-oriented companies across industries stay ahead of the curve by leveraging its world-class talent of over 11,700+ full-time Movators across 20 global locations and a gig network of thousands of technology experts across 60 countries, speaking over 100 languages.